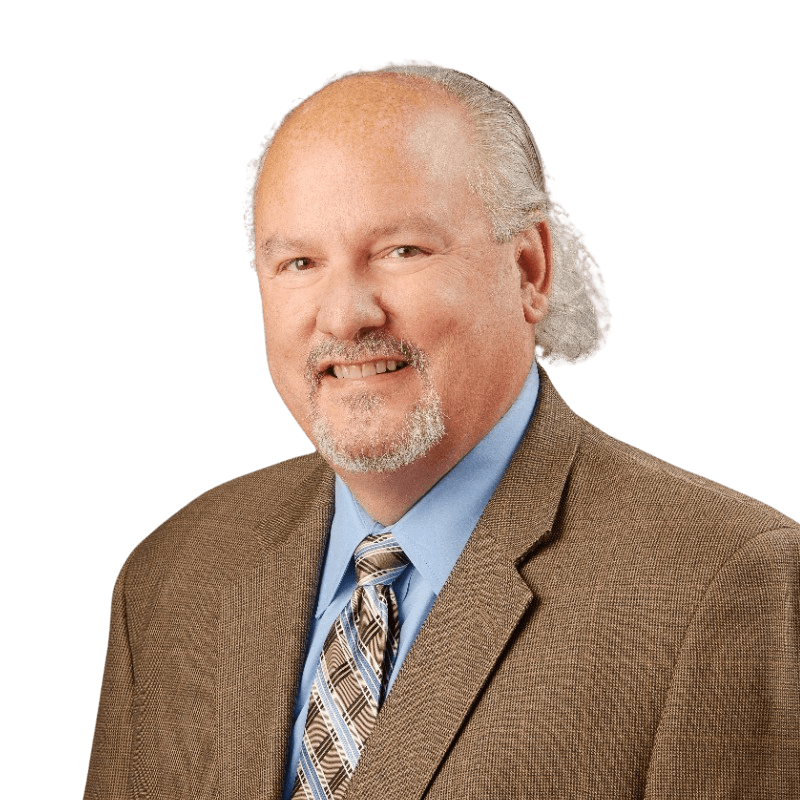
RHP Risk Management’s Rod Harvey, PE, CIH, CSP, CHMM, will present on “Validating OSHA’s Proposed Heat Stress Acclimatization Schedule” on September 16, 2025, at the Chicagoland Safety, Health & Environmental Conference in Naperville, IL.
This timely presentation comes at a critical juncture, as OSHA advances its efforts to implement the first-ever federal standard addressing heat injury and illness prevention in both indoor and outdoor occupational settings. Mr. Harvey will provide an authoritative overview of the acclimatization protocol included in OSHA’s proposed rule.
Study Highlights: Evaluating the OSHA Acclimatization Schedule
RHP’s scientific study evaluated eight healthy volunteers in a controlled environment using wearable technology. Participants were exposed to progressively longer durations of heat stress over five days, simulating OSHA’s model.
Key findings include that, on average, there was a reduction in both heart rate and core body temperature after following the schedule. While baseline measurements prior to heat exposure showed no significant differences, post-exposure data demonstrated that progressive heat acclimatization supported physiological adaptation in most participants. The reduction in both heart rate and core body temperature were not statistically significant, however, the variability in individual responses highlighted the importance of flexible, monitored approaches.
Mr. Harvey’s presentation at the Chicagoland Safety, Health & Environmental Conference provides a unique opportunity to explore the scientific basis of OSHA’s acclimatization schedule.
Attendees will gain practical and valuable insights into integrating validated acclimatization strategies into workplace heat stress programs, applying real-world data, and preparing for upcoming regulatory requirements.
Current Status of OSHA’s Proposed Heat Injury Standard
In response to rising concerns about worker exposure to extreme heat, OSHA advanced efforts toward a formal standard in August 2024 by issuing a Notice of Proposed Rulemaking (NPRM) for the Heat Injury and Illness Prevention in Outdoor and Indoor Work Settings rule. The rule has since entered the final stages of rulemaking, including virtual public hearings that commenced in June 2025.
Under the previous administration, a final rule was anticipated by early 2026, requiring employers to implement a written Heat Injury and Illness Prevention Plan (HIIP) that included environmental monitoring, access to hydration, rest and shade, and a phased acclimatization process. OSHA’s proposed schedule outlines a progressive five-day heat exposure ramp-up—starting with 20% of typical exposure on day one and reaching 100% by day five. To date, the current administration has maintained this rulemaking timeline. Currently, OSHA is utilizing its National Emphasis Program (NEP) and General Duty Clause to proactively inspect high-heat workplaces.
How Can Employers Prepare for the Proposed Heat Injury Standard?
Six states (California, Colorado, Maryland, Minnesota, Oregon and Washington) have already implemented their own heat standards, offering reference models for employers. The proposed federal OSHA rule is expected to apply at temperatures of 80°F and above, with additional protective measures required at 90°F. Compliance will rely heavily on real-time monitoring and robust recordkeeping practices.”
Here are 10 key actions employers can take to prepare for OSHA’s heat injury standard:
- Learn from State-Level Standards: Review and adapt best practices from the states that have already implemented heat safety regulations.
- Develop or Update a Written HIIPP: Create or revise a comprehensive Heat Injury and Illness Prevention Plan (HIIPP) that includes specific heat index triggers and mitigation strategies. Address key elements such as hydration access, rest periods, shaded recovery areas, emergency response, and acclimatization protocols.
- Implement a Phased Acclimatization Program: Adopt OSHA’s phased acclimatization model or other steps to acclimatize workers. OSHA’s phased exposure approach includes:
- New workers: begin at 20% of the typical exposure duration on day 1; increasing by 20% daily.
- Returning workers: begin at 50% exposure, progressing to full exposure over 4 days.
- Train all personnel in heat illness recognition and prevention. Provide training on recognizing and preventing heat-related illnesses, with emphasis on self-monitoring and reporting. Tailor content to meet the language and literacy needs of your workforce.
- Monitor environmental conditions. Use tools to measure the heat index or Wet Bulb Globe Temperature (WBGT) and implement protective measures when thresholds are exceeded. For conditions above 90°F, include mandatory rest breaks and increased supervision.
- Use wearable tech for real-time heat exposure tracking: Deploy wearable devices to monitor real-time heat exposure, helping to protect individual workers and inform intervention strategies.
- Designate Heat Safety Coordinators. Assign trained personnel to oversee heat safety compliance, coordinate emergency responses, and manage acclimatization tracking.
- Apply Engineering and Administrative Controls.
- Engineering controls: Air conditioning, fans, misting or cooling stations, task automation, and enhanced ventilation.
- Administrative controls: Modified work-rest cycles, acclimatization programs, job rotation, hydration breaks, scheduling during cooler hours, training and education, monitoring, and clear emergency response plans.
- Maintain records and assess program effectiveness. Track training participation, incident reports, temperature exposures, and acclimatization records. Use data to evaluate and improve program performance while demonstrating compliance.
- Stay informed and prepare for enforcement: Monitor OSHA’s rulemaking process, stay current on regulatory updates, and proactively align your heat safety programs with anticipated requirements.
Contact RHP Risk Management to Reduce the Risk of Heat Stress in Your Workplace
As climate change drives increasingly hazardous heat conditions, OSHA’s forthcoming rule signals a paradigm shift in occupational health expectations. Organizations that begin aligning with the proposed framework now — especially around acclimatization and monitoring — will be well-positioned for compliance and improved worker protection. Contact RHP Risk Management’s staff of experienced Industrial Hygienists who provide guidance to employers implementing occupational health and safety plans.
For more on RHP’s expertise in heat stress, watch Rod Harvey’s, P.E., CIH, CSP, CHMM interview with Business Insurance on how heat events can elevate property and liability risks and risk management steps can be taken to mitigate heat events; listen to Rod’s discussion on the Missouri Employers Mutual podcast about the warning signs of heat stress, employee training, and solutions to working in hot conditions; and listen to Rod’s appearance on the Greenberg Traurig podcast to discuss OSHA’s National Emphasis Program related to heat hazards, effective employer prevention strategies, controls, training and occupational heat stress litigation.
Contact RHP for an initial consultation or call (866) 481-8188.